Great performance on the plastic injection process.
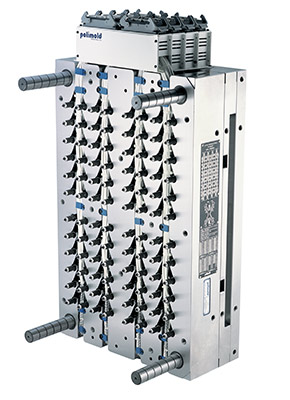
More Information

Fast, safe and with good performance on the injection. Recommended to parts of different sizes and applications.
The Thermal Gate Hot Runner System is made of a Fully balanced manifold, nozzles, set up with tips and electrical box.
We have a diverse line of standard components to facilitate the manufacturing of the tool. We also develop special items according to your product’s needs.
Main advantages Conventional Hot Runner System:
- Less raw material, free of tensions and thermally homogeneous.
- Less pressure on the plastic injection, resulting on more precision.
- Easy processing on the injection of materials.
- Faster and more precise cycles.
- Versatile and flexible on product’s color change.
Polimold has various hot SPRUES dimensions for the APPLICATION according to the needs of the product. Please get to know the available series on the market:
SERIE | LINE | INDICATION | IMAGE |
25 | POLIFAST | High productivity molds with small parts (weight up to 30g *) with limited physical space. injection of commodity materials(PP, PE, PS). | ![]() |
50 | POLIFAST | High productivity moulds with small parts (weight up to 80g *), with a R.O.I. better than 25 series. Injection of commosity materials (PP, PE, PS). | ![]() |
FASTMAX | High productivity molds with small parts (weight up to 30g *), with limited physical space. Applied in materials where the injection temperature is slightly higher than in commodity materials (ABS, POM, Polyamide without Load, among others). | ![]() |
|
POLIMAX | High productivity molds with small parts (weight up to 30g *), with the limited physical space. Applied to materials in which the injection temperature is slightly higher than in commodity materials (abs, pom, polyamide without load, among others). | ![]() |
|
200 | POLICOSMETIC | Small to medium size parts (weight up to 180G *) with minimal vestige (cosmetic finish). Injection of commosity materials (PP, PE, PS). | ![]() |
POLIMAX | Small to medium size parts (weight up to 180g *). have variety of tips. suitable for injection of engineering materials, but can also inject commodity materials when provided the correct tip, for this kind of application look for our technical department. | ![]() |
|
500 | POLICOSMETIC | Midsize parts (weighing up to 300g *) with minimal vestige (cosmetic finish). Injection of commosity materials (PP, PE, PS). | ![]() |
POLIMAX | Medium size parts (weight up to 300g *). Have variety of tips. suitable for injection of engineering materials, but can also inject commodity materials when provided the correct tip, for this kind of application look for our technical department. | ![]() |
|
800 | POLICOSMETIC | Medium to large parts (up to 500g * weight) with minimal vestige (cosmetic finish). Injection of commosity materials (PP, PE, PS). | ![]() |
POLIMAX | Medium to large size parts (weight up to 500g *). Have variety of tips. suitable for injection of engineering materials, but can also inject commodity materials when provided the correct tip, for this kind of application look for our technical department. | ![]() |
|
1000 | POLICOSMETIC | Large parts (more than 1000g * weight) with minimal vestige (cosmetic finish). Injection of commosity materials (PP, PE, PS). | ![]() |
POLIMAX | Large size parts (more than 1000g *). Have variety of tips. Suitable for injection of engineering materials, but can also inject commodity materials when provided the correct tip, for this kind of application look for our technical department. | ![]() |
The Polimold Hot Runner System is recommended to plastic injections in a large numbers of industries, such as: automotive, packing, cosmetics, electronic devices, toys, construction, among others. Please check below some examples of the application of Standard Hot Runner System.
Gallery
Polimold is fueled by the challenge of creating products that exceed the expectations of clients! Check a few of our cases using the Standard Hot Runner System.
Bi Injection +
![]() | Name of the part: Column Structure A |
Material: PA 6/ TPE | |
Weight: 373g piece in PA 6 139g piece in TPE | |
Cavities: 2 + 2 | |
Injection Points: 6 points for TPE / 4 points for PA | |
Injection: Standard Hot Runner System – Two-Injection model | |
Serie: 200 | |
Line: Polimax |
Polimold Solution: The client’s request was to inject parts with different materials on the same mold.
We developed a system with two different manifolds, one with a lateral input for the injection of TPE and the other input centered for the injection of material PA 6.
Stack Mold +
![]() | Name of the part: Spacer |
Material: PE AD | |
Weight: 10 g | |
Cavities: 64 (32 + 32) | |
Injection Points: 32 + 32 | |
Injection: Conventional Hot Runner System – Stack Mold | |
Serie: 200 | |
Line: Policosmetic |
Polimold Solution: In this case, we had to increase the productivity of the mold using a single injection tool on a small-sized machine.
We developed a conventional stack mold injection system to produce parts on both sides of the mold.
The great challenge of this project was on the closing section of the mold, where we predicted the material could purge, causing trouble on the mold closing. we choose a valve gate sprue bushing with a valve gate feeder bushing, without changing the main idea of the project.
Injection with Surlyn+
![]() | Name of the part: Perfume Cap |
Material: Surlyn | |
Weight: 22 g | |
Cavities: 8 | |
Injection Points: 4 | |
Injection: Standard Hot Runner System – “Sobre Canal” Model | |
Serie: 200 | |
Line: Polimax |
Polimold Solution: For the injection of surlyn, where the injection pressure is higher than compared with other materials, the polimold engineering developed an injection system where the nozzles are threaded in the manifold, preventing possible leaks of raw material.
Perfect Balance +
![]() | Name of the part: Fan Grill |
Material: PP | |
Weight: 662 g | |
Cavities: 2 | |
Injection Points: 12 | |
Injection: Standard Hot Runner System – Bridge Model | |
Serie: 500 | |
Line: Policosmetic |
Polimold Solution: Our client’s request had a very complex location for the injection points. The main goal was to develop a system that allows the uniform filling of the cavities, keeping the internal balance of the manifold’s FLOW CHANNELS.
We created a manifold splitted in the sections, two of them with six injection points (each) and above these ones a manifold linking these sections.
By using this layout, not only we established a perfect balance for the cavities, but also avoided an excessive thermal expansion of the manifold, which would cause the rupture of the threaded nozzles.